DataScope
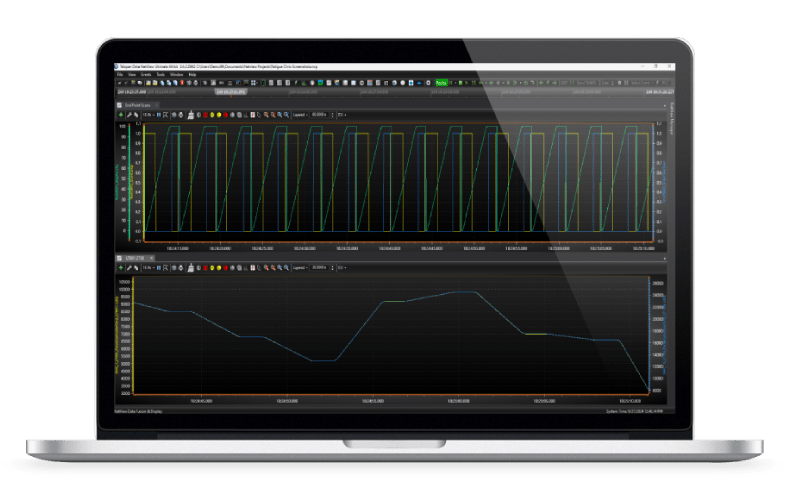
DataScope – Data Fusion for the next generation structural test environment
Traditionally, structural test facilities have been using a Load Control Systems (LCS) and Data Acquisition Systems (DAS) which relies on foil type gauges for load and stress measurements. The DAS will often combine position and displacement transducers like string pots and LVDT’s. The integration between the LCS and DAS has been mostly adequate for this type of testing. In recent years though, Structural Test Engineers have started to utilize “new sensor” technologies like the Fiber Optic Strain (FOS) and Digital Image Correlation (DIC).
Deploying all these systems into an existing test facility has given test engineers new tools, but their deployment has led to a composite assembly of hardware systems, data sets and dedicated single-task software. At the test facility level, these new capabilities come with a need for more operators to set up and monitor, as well as long processing times (if at all possible) to align the various sources of data before handing it over to analysts.
Data Fusion is the process of integrating multiple data sources to produce more consistent, accurate, and useful information than that provided by any individual data source. DataScope & NetView Data Fusion & Display software was used in the design and implementation of a large-scale structural test system based on an aerospace industry open standard – IRIG 106 Chapter 10. CH10 covers all critical aspects of handling data: synchronization of multiple sources, recording and simultaneous distribution for real-time display.
Traditionally, hardware used in ground test facilities outputs a proprietary data stream and not CH10 natively. Derived from an airborne product, the iGU (instrumentation Gateway Unit), Telspan Data provided the gNGU (ground Network Gateway Unit) as a configurable “gateway” between the proprietary data streams and the CH10 data processing capabilities of NetView. Telspan wrote special CH10 data converters for the LCS, DAS, FOS and DIC and used a gNGU for the data conversion. The Telemetry Attributes Transfer Standard (TMATS) is used to transfer each and every channel specific information from each and every system. This contains the EU conversion, upper/lower warning/alarm levels, channel names/descriptions, etc. which is also broadcast on the network, as well as recorded as part of the file in .ch10 format.
With the proprietary data formats from each system time stamped, converted to CH10 and broadcast on the network, the data is now aggregated into one single stream by the NetView Data Host. Acting as a central point for all data, the Data Host time aligns the streams for recording and distribution. Considering the large amount of data and very long test duration (months or years), the Data Host is connected to a dedicated Network Attached Storage (NAS) where continuous time history and “single scan” data recording are stored. The architecture adds redundancy to the critical recording function by having all the data sources independently record their own data on their respective systems. In addition to aggregating the data for recording, the Data Host simultaneously provides a UDP broadcast of the data stream for real-time analysis
With Data Fusion, Analysts have a completely new way of looking at data with the NetView Data Client. Instead of discretely looking at one systems data stream, Data Client can display any channel from any system on any real-time display. Real-time displays include XY Plot, Tabular, Bar Chart, Line Graph, Strip Chart, etc. and include warning/alarm limits, prediction lines and are individually customized to each analyst’s workstation. Any one display can also fuse measurements of several sources to refine the analysis; for example data from foil Strain Gage and Fiber Optic System can be combined to complement, improve or simply compare to increase confidence in the findings.
Since all data from all systems is now available as a single stream, this give test conductors and analysts a whole new level of real-time capability. Specific to this large-scale structural test the Data Distributor will also add other real-time functions like trend analysis, strain surveys, strain prediction/comparison, go/no go end-point averaging, etc. These functions help to reduce test time by automating many of the functions the analysts would have done manually in the past
This innovative architecture provides a new class of performance for the next generation ground test facilities since it is based on open standards, technologies, and products that are readily available. Other sources of data are easily added with systems that provide native Chapter 10 data stream or a Telspan gNGU is utilized. Data Fusion is more than just combining data from multiple sources. Data Fusion gives the Test Designers, Test Conductor, Test Engineers and Analysts a suite of new capability; all recorded data from all systems in the same format, all sources data available for display on a single GUI for real-time and post processing was all the more critical in this implementation because of the sheer scaleof this testing. It would certainly add a lot of efficiency to much smaller scale, where the architecture described could be limited to one computer running NetView to cover collection, recording and distribution.